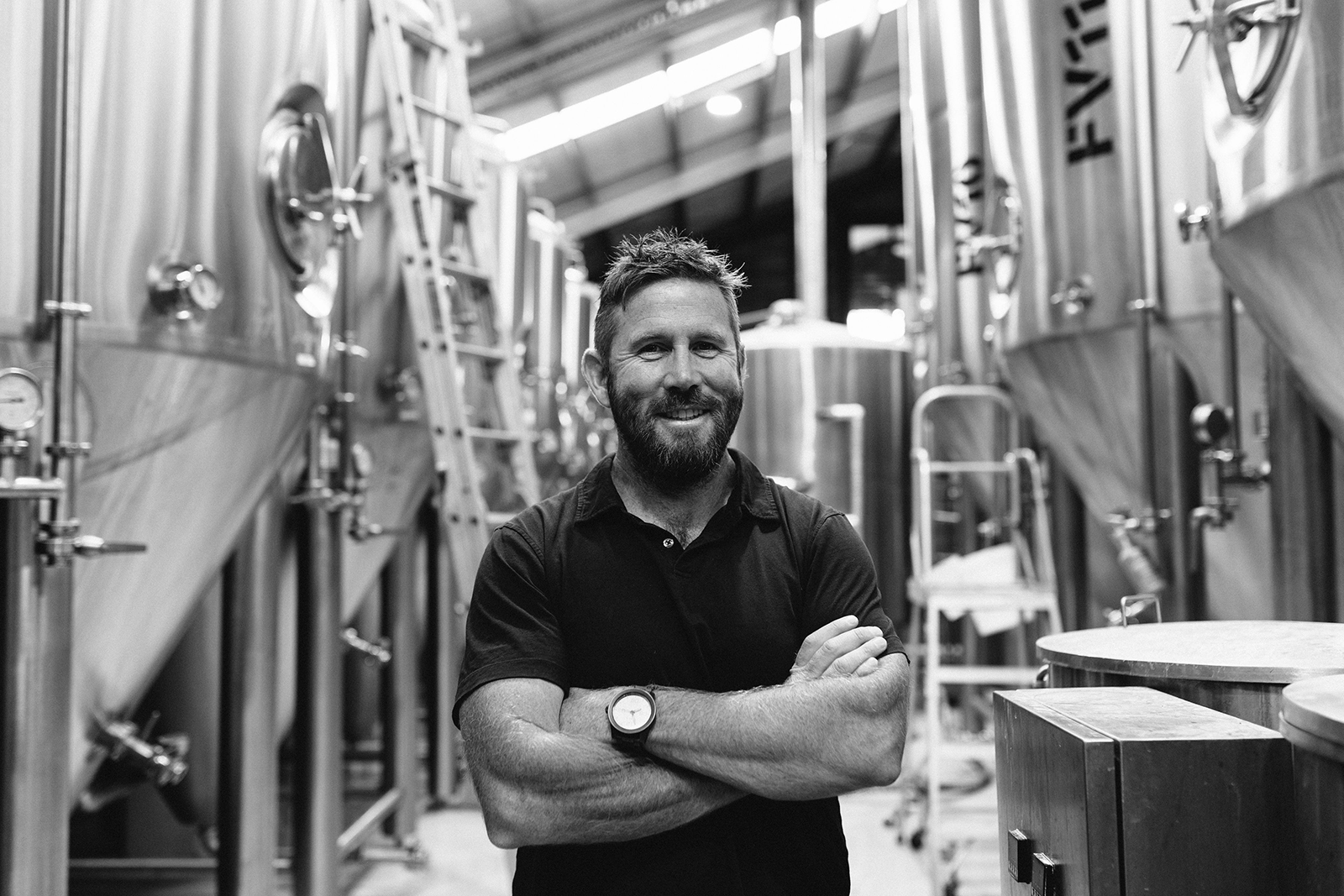
Matakana – A brewery at Matakana in Northland, is making big environmental changes to the way their beer is being produced.
Sawmill brewery owner Mike Sutherland he needs to commit to make the climate changes needed.
Sawmill Brewery has been operating in Matakana for 17 years and has made sustainability and efficiency a core part of their identity.
They are New Zealand’s first, and only, B-Corp certified brewery and have introduced initiatives and changes to their operations that are leading the way for their peers.
Sawmill Brewery is currently completing an energy transition plan which will help the brewery make informed investment decisions to support their decarbonisation journey.
Through the project, technically and commercially viable options have been mapped to reduce energy-related emissions of the existing brewhouse over the next 20 years..
Over the next six months, Sawmill will be reviewing the findings of the study and working towards implementing their preferred option.
12 years in the competitive New Zealand craft beer industry which now consists of over 200 Kiwi businesses has given Sutherland an appreciation for the creative and innovative nature of brewers.
Craft beer has continued to push the boundaries in terms of style and flavour, to the point where there isn’t much more to change.
“To me, it is important that our industry moves now, to support the positive change we need to look after people and our environment.”
In addition to reducing reduction and conserving, Sawmill has optimised and improved its processes to improve energy efficiency and reduce the demand for fossil fuels.
The installation of a heat recovery system at the brewery saves around 1.5 million litres of water and 6000 kg of LPG every year, by recycling the water used to chill wort back into the hot water tank.
Solar panels installed in 2019 were also generating up to 97 percent of the breweries power, prior to a brewery fire in 2019 which damaged the system.
The main energy consuming operations at the Matakana site are related to beer production and refrigeration processes. LPG, used in both the brewery and kitchen, is responsible for most of the site’s energy related emissions, and accounts for 65 percent of overall energy consumption. Electricity is used for other processes such as cooling, pumping liquids, and running equipment.
The findings of the project have outlined relative costs and return on investment as well as opportunities for energy efficiency and fuel switching.
Energy efficiency opportunities include a potential transformer upgrade, the reinstallation of solar PV with additional capacity, kettle vapour heat recovery, and the installation of energy efficient GEA equipment.
Alternatively, fuel switching opportunities include biogas cofiring with LPG in the existing boiler or replacing the existing boiler with a new 500kW electric version.